Offshore operations present unique challenges and demands on equipment due to the harsh and corrosive marine environment. Hydraulic rotary actuators are crucial in various offshore applications, providing reliable and efficient motion control. In this article, we will explore the specific requirements that hydraulic rotary actuators must meet to ensure optimal performance and longevity in offshore operating environments.
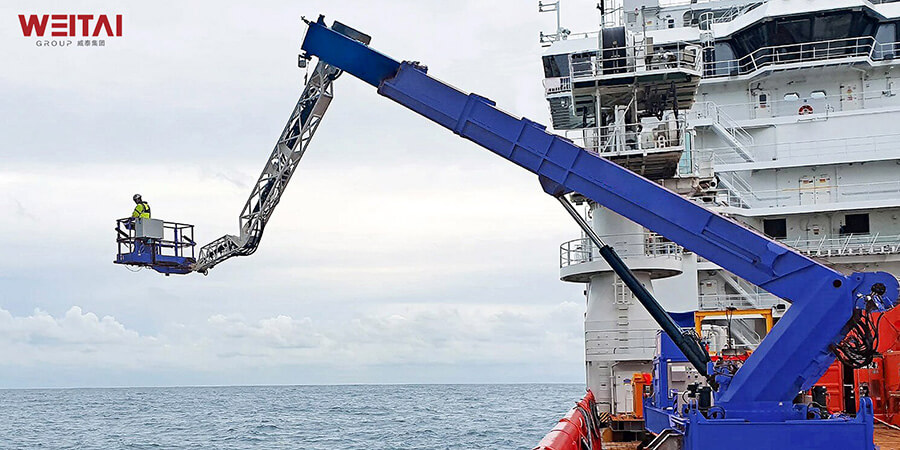
Corrosion Resistance
One of the primary requirements for hydraulic rotary actuators in offshore environments is corrosion resistance. The exposure to saltwater, humidity, and aggressive chemicals necessitates the use of materials that can withstand corrosion. Actuators constructed from corrosion-resistant alloys, such as stainless steel or specialized coatings, are essential to ensure the longevity and reliability of the equipment.
Sealing and Protection
Offshore environments are subject to challenging conditions, including water ingress, high pressures, and extreme temperatures. Hydraulic rotary actuators must be effectively sealed and protected to prevent damage and maintain optimal performance. Seals and gaskets must be designed to withstand the corrosive effects of seawater and provide reliable protection against water and contaminants.
Reliability in Harsh Conditions
Offshore operations often involve heavy loads, strong vibrations, and shocks. Hydraulic rotary actuators must be designed to withstand these harsh conditions and maintain their functionality and precision. Robust construction, reinforced bearings, and specialized damping systems are essential to ensure reliable operation and minimize the risk of failure.
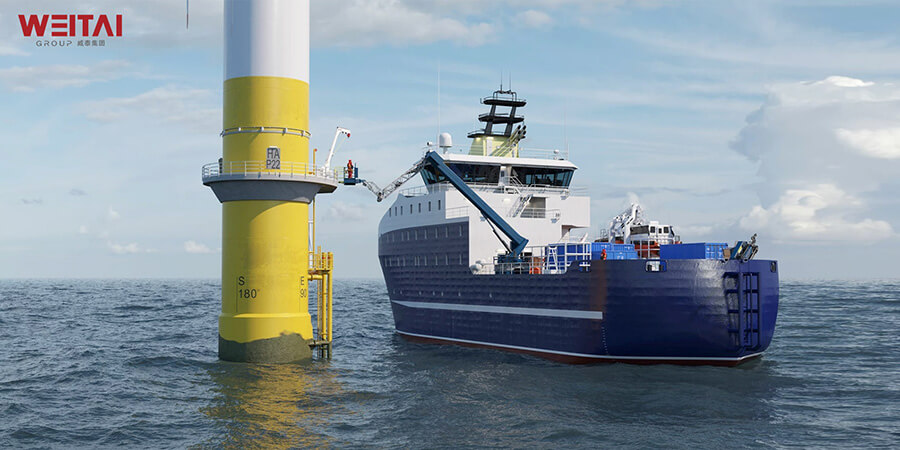
High Performance
Offshore applications often require high torque and precise control. Hydraulic rotary actuators must deliver the required torque output to perform tasks such as valve control, positioning of heavy equipment, or subsea manipulations. The actuator's design and hydraulic system should be optimized to provide high power density and responsiveness while maintaining accuracy and repeatability.
Environmental Adaptability
Offshore environments can vary significantly, ranging from calm waters to extreme weather conditions. Hydraulic rotary actuators should be adaptable to these changing conditions and be designed to operate effectively across a wide range of temperatures, pressures, and humidity levels. This adaptability ensures consistent performance and minimizes the need for equipment replacement or maintenance.
Ease of Maintenance
In offshore operations, equipment downtime can be costly and challenging to manage. Hydraulic rotary actuators should be designed with ease of maintenance in mind. Accessible inspection points, replaceable components, and clear maintenance procedures can help reduce downtime and enable efficient servicing, ensuring the longevity and reliability of the actuators.
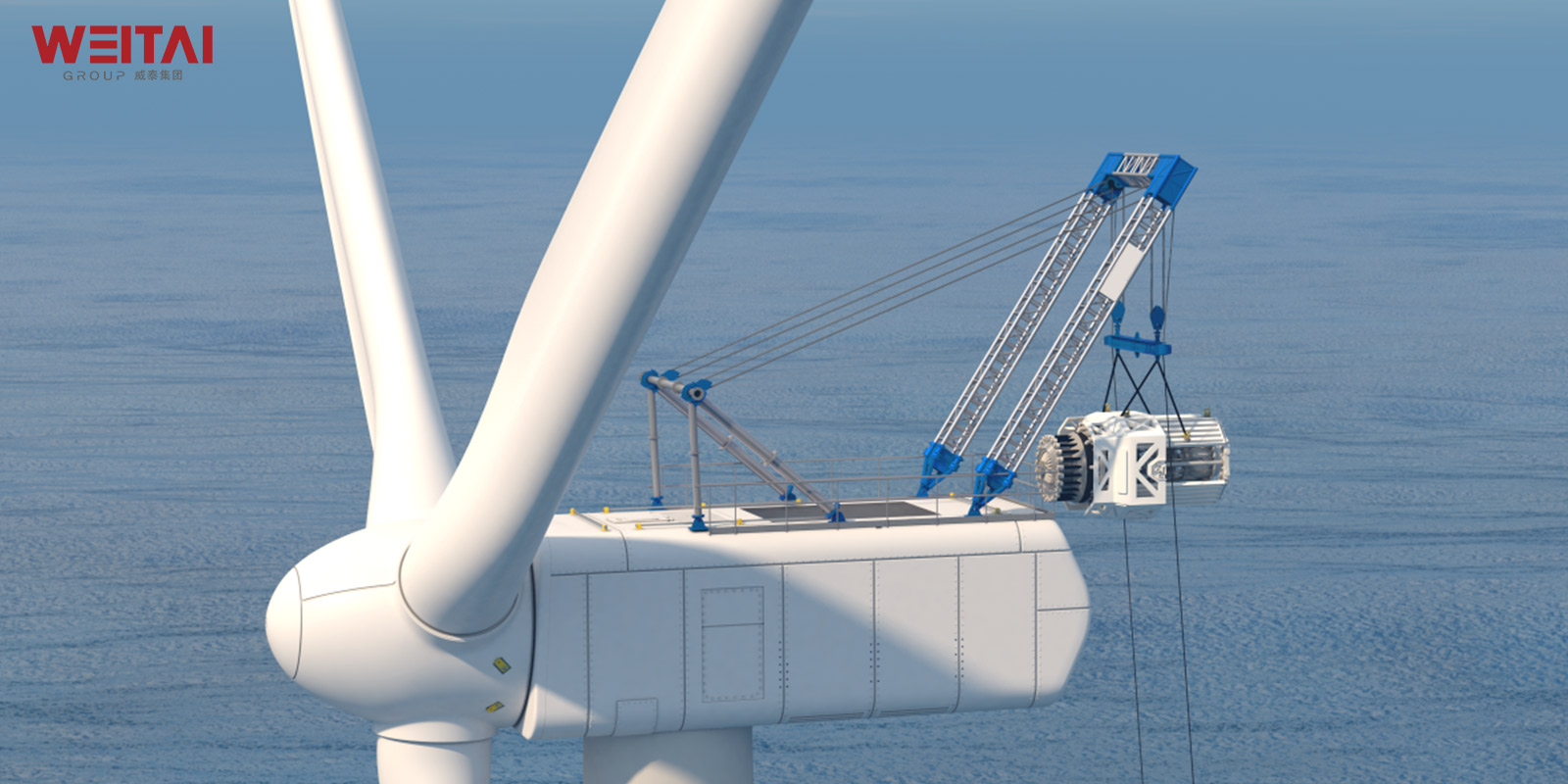
Compliance with Industry Standards
Offshore operations are subject to stringent safety and regulatory standards. Hydraulic rotary actuators must comply with industry-specific certifications, such as those related to marine and offshore equipment. Compliance with these standards ensures that the actuators meet the required performance, reliability, and safety requirements for offshore applications.
Designing and manufacturing hydraulic rotary actuators to meet the quality standards required for offshore operations involves careful consideration of several factors. The following are key steps and practices to ensure the quality of hydraulic rotary actuators that can meet the standards for offshore use:
Robust Design
The design phase plays a critical role in ensuring the quality and reliability of hydraulic rotary actuators. Robust design practices, such as thorough analysis and simulation, enable engineers to anticipate and address potential issues early on. Factors such as load capacity, torque requirements, environmental conditions, and operational parameters should be carefully considered during the design process.
Material Selection
Choosing the right materials is crucial for ensuring the longevity and corrosion resistance of hydraulic rotary actuators in offshore environments. Corrosion-resistant alloys, such as stainless steel or specialized coatings, should be selected to withstand the harsh marine conditions. Material selection should also consider factors like strength, durability, and compatibility with hydraulic fluids and seals.
Quality Manufacturing Processes
Adhering to strict manufacturing processes is essential for ensuring the quality of hydraulic rotary actuators. This includes employing advanced machining techniques, such as precision CNC (Computer Numerical Control) machining, to achieve tight tolerances and accurate component dimensions. Manufacturing processes should follow recognized standards, such as ISO 9001, to ensure consistent quality throughout the production cycle.
Testing and Inspection
Rigorous testing and inspection procedures are critical to verify the performance and reliability of hydraulic rotary actuators. These tests may include pressure testing, endurance testing, torque measurement, and functional testing under simulated offshore conditions. Non-destructive testing techniques, such as ultrasound or X-ray inspection, can also be employed to detect potential defects or flaws in critical components.
Compliance with Standards and Regulations
Hydraulic rotary actuators used in offshore operations must comply with industry-specific standards and regulations. These standards may include certifications such as API (American Petroleum Institute) standards, ABS (American Bureau of Shipping) certifications, or ISO 15552 for pneumatic actuators. Compliance with these standards ensures that the actuators meet the required safety and performance criteria for offshore applications.
Documentation and Traceability
Maintaining thorough documentation and traceability throughout the design and manufacturing process is essential for quality control. This includes recording materials used, manufacturing processes employed, and test results obtained. Proper documentation enables the traceability of each actuator and facilitates the identification of any issues that may arise in the future.
Continuous Improvement
Implementing a culture of continuous improvement is crucial for maintaining and enhancing the quality of hydraulic rotary actuators. Feedback from field operations and customer feedback should be considered to identify areas for improvement. Regular reviews of manufacturing processes, quality control procedures, and material selection can lead to iterative refinements that improve the overall quality and reliability of the actuators.
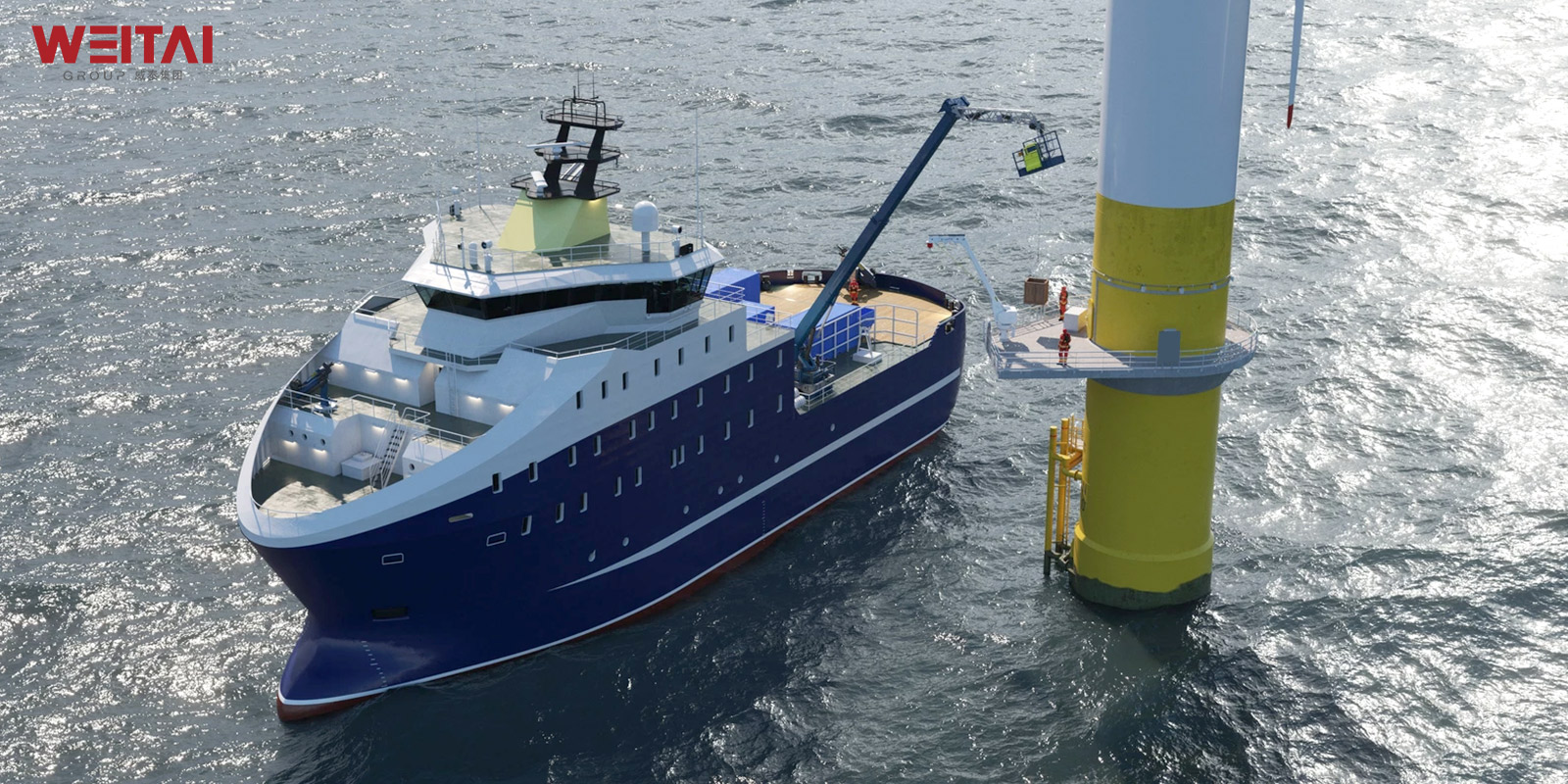
By incorporating these practices into the design and manufacturing processes, hydraulic rotary actuators can be manufactured to meet the quality standards required for offshore operations. Adherence to robust design principles, careful material selection, rigorous testing, compliance with industry standards, and continuous improvement efforts all contribute to the production of high-quality hydraulic rotary actuators capable of withstanding the demanding conditions of offshore environments.
In conclusion, hydraulic rotary actuators used in offshore operating environments must meet specific requirements to withstand the challenges posed by the marine environment. Corrosion resistance, effective sealing, reliability in harsh conditions, high performance, environmental adaptability, ease of maintenance, and compliance with industry standards are crucial considerations. By meeting these requirements, hydraulic rotary actuators can provide reliable and efficient motion control in offshore applications, contributing to the success and safety of offshore operations.